3D Printing Phoenix AZ is a radically different manufacturing process that builds up parts additively, layer by layer. This allows for faster prototyping, saving time and money versus traditional subtractive techniques.
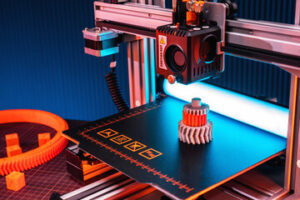
Engineers can use 3D printers to quickly turn CAD models into physical prototypes, cutting development time by weeks or months. For example, GE Aviation used a 3D-printed Cobalt-Chrome fuel nozzle, which was 25 percent lighter and five times stronger than conventional ones.
Additive manufacturing is a process that converts digital inputs—such as computer-aided design files of industrial parts—into tangible 3D objects. This is different from traditional “subtractive” manufacturing methods, which work by shaping an object out of stock materials. This technique is also known by the name freeform fabrication, layer-based manufacturing, additive layer production, and additive layer synthesis.
Using additive printing, manufacturers can create complex products in a much shorter time than with conventional technologies. They can also customize these products to suit specific needs. These benefits have led to increased adoption of additive technology in a variety of industries, from medical to automotive. Additive technology also allows companies to build prototypes in-house and reduce the risk of relying on third parties for production.
The additive manufacturing process has the ability to create structures with complex geometry and can handle a wide range of materials. Polymeric materials (such as plastics and nylon) are most common, but metals can also be printed. These capabilities make additive manufacturing a powerful tool for reducing the cost and time of producing custom products.
With the advent of advanced 3D printers, manufacturers can print a part in one step, rather than in several steps. Many of these “smart” machines are capable of storing large volumes of data during the fabrication process, which is then used by AI to automate processes and improve prints. This feature has reduced production times, lowered material consumption, and allowed manufacturers to monitor printer performance and usage metrics.
In addition to reducing costs, additive manufacturing is a great way to make prototypes of products, which can be used for testing and training. It can also help designers avoid costly mistakes, reduce development and manufacturing time, and increase the flexibility of their designs. Additionally, additive manufacturing is a great tool for creating parts that are difficult to machine.
Additive manufacturing can be used to produce a wide range of medical products, including prosthetics and surgical tools. It can also be used to manufacture replacement parts for older devices. It can also be used to produce customized orthotics and insoles for patients with diabetic foot problems or inflammatory arthritis.
Rapid prototyping
When developing a new product, it is important to have a way to test the functionality and performance of the finished product. This is where rapid prototyping comes in. Using 3D printing technology, engineers can quickly produce physical models of their design, allowing them to see how the finished product will look and work. This helps them identify any potential flaws in the final product and correct them before moving to production.
This prototyping technique is often used in various industries, including manufacturing, engineering, and architecture. Universities are also increasingly turning to this technology to teach students how to use it. Some even offer specializations in additive manufacturing for students interested in careers in these fields.
While traditional methods for producing prototypes are expensive, 3D printing is fast and cost-effective. It allows companies to produce prototypes quickly and efficiently, reducing the time it takes to complete the product development process. This allows businesses to get their products into the hands of customers faster and improve customer satisfaction.
The rapid prototyping industry has experienced robust growth over the past five years, boosted by technological advancements and new applications. As the technology advances, it is likely that it will become even more efficient and accurate than traditional methods. Industry revenue is expected to reach $4.3 billion by 2024, a significant increase from its estimated $1.9 billion in 2020.
Historically, product designers and engineers relied on simple tools to create proof of concept models for new designs. These prototypes were crude and often had errors in size, weight, and finish. Using traditional manufacturing processes, these errors could be costly when the product moved to production. Fortunately, 3D printing is now making it possible to produce high-fidelity prototypes that resemble the finished product, eliminating many of the risks associated with new products.
The first step in the rapid prototyping process is to create a prototype based on CAD data. This is a good way to get feedback from users and identify issues that need to be addressed. This feedback should be consolidated and analyzed to identify key themes and trends. Then, the prototype can be redesigned to meet the user’s needs.
Customization
3D printing is a powerful technology that can be used to create customized products that meet the needs and preferences of individual users. This customization has led to an increase in customer satisfaction and improved user experiences. In addition, it has allowed businesses to differentiate their products from those of their competitors and gain a competitive advantage.
Customization is a key element of mass customization, and 3D printing is at the forefront of this movement. It allows businesses to produce personalized products for their customers, making them feel like they have a unique connection to the product. This can increase customer satisfaction, loyalty, and brand loyalty. It can also improve the company’s bottom line by reducing production costs and minimizing inventory and distribution costs.
Unlike traditional manufacturing methods, which rely on blocks of material and molds to make physical objects, additive 3D printing involves layering and fusing together layers of material to produce parts. This process is fast, affordable, and flexible. It can produce complex geometries that are impossible to create with conventional manufacturing techniques and can be made from a variety of materials. This versatility and affordability have made additive manufacturing an attractive production method for many companies.
According to a recent survey by Jabil, 46% of respondents say that additive manufacturing reduces their direct and indirect production costs. This includes cost savings on everything from capital purchases to tool costs and productivity. Moreover, it can reduce assembly time and inventory costs, as well as provide significant savings on logistics and shipping. The use of additive manufacturing can also improve the quality and performance of products, resulting in substantial savings on repair and replacement costs.
Adding customization capabilities to 3D printing can open up endless possibilities for manufacturers. Whether it’s adding intricate internal structures, personal branding elements, or serialization, businesses can customize their parts for specific purposes and requirements. It can also help them achieve greater design freedom, which can result in higher performance parts, reduced part consolidation, and improved material efficiency. For example, a manufacturer can use design optimization software to optimize foot insoles for each individual client, which can lead to increased strength-to-weight ratios and improved comfort.
Sustainability
Over the past few decades, alarm about the impact of human activities on the environment has steadily risen. Among the major concerns is the massive amount of natural resources consumed in manufacturing processes and the vast amounts of waste they produce. 3D printing is an innovative technology that offers a viable solution to these problems. Unlike traditional manufacturing methods, 3D printing uses very little water and consumes only the energy needed to heat the printing material and operate the printer. Moreover, 3D printing does not emit any toxic chemicals. Thus, this technology can greatly reduce the environmental footprint of manufacturing.
In addition to reducing the carbon footprint of manufacturing, 3D printing also allows manufacturers to reuse the printing materials for future prints. This process is known as filament recycling and is an important aspect of sustainability. Many companies are already utilizing this technology to reduce the cost and environmental impact of their products.
One example of this is the Markforged Metal X, which uses recycled aluminum as its building block. Its resulting structure is stronger than conventional metal, and it uses only 10% of the energy required for CNC machining. It can be used in a wide variety of applications, including aerospace engineering and medical implants.
Additionally, 3D printing eliminates the need for complex manufacturing plants and shortens supply chains. This reduces the need for fossil-fuel-hungry logistics bridges and reduces waste materials. Additionally, 3D printing can be done locally, which reduces costs and reduces social and environmental inequity.
As the technology evolves, it is likely to make significant impacts in various environmental applications. For example, it can be used to create separation devices, sensors, and alternative energy technologies. It can also be used to monitor air quality, detect water and biological contaminants, and as a safeguard tool during a COVID-19 pandemic.
While these benefits of 3D printing are promising, there are some issues to consider before implementing it for sustainable use. First, manufacturers need to choose a more sustainable printing material. Currently, most printable materials are made of non-biodegradable polymers. Some are even made from petroleum. However, some manufacturers are now offering a range of green materials for use with 3D printers, including bio-based and biodegradable polymer blends, recycled plastics, and waste materials from other industries.